The most common NDT techniques include
Radiography (X-rays and gamma rays): Uses radiation to detect internal flaws, such as cracks and voids. It is particularly useful for inspecting welds and dense materials.
Ultrasound: Involves sending high-frequency acoustic waves into the material and measuring the time it takes for these waves to return. It allows for the detection of internal flaws and is highly accurate for thickness measurements and defect location.
Magnetic Particle Testing: This technique is recommended for ferromagnetic materials. It consists of applying fine particles to the surface of the material. It will cluster in areas where there are surface or subsurface flaws.
Eddy Currents: Based on the principle of electromagnetic induction. This technique is primarily used to detect surface flaws in conductive materials.
Dye Penetrant: Consists of applying a dye to non-porous materials. After the dye penetrates the surface flaws. It is possible to visualize the presence of defects by removing excess dye and applying a developer.
Each technique has its advantages and limitations, and the choice of the appropriate method depends on the type of material. The geometry of the part, the type of defect sought, and the environmental conditions.
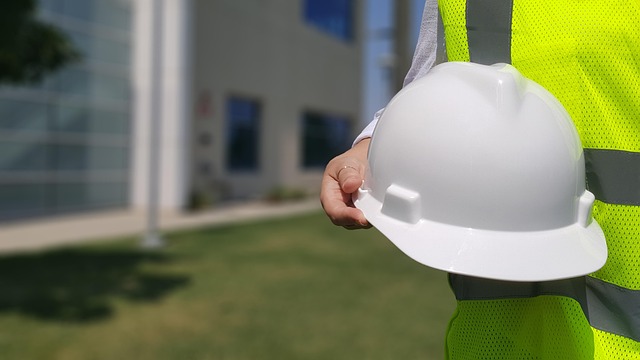
Industrial Applications and Importance of NDT:
Non-destructive testing plays a crucial role in several industries. Some examples of its applications include:
Aeronautics: Safety in the aviation industry depends on rigorous maintenance and non-destructive testing to detect structural flaws in fuselages and critical aircraft components.
Construction: Tests such as ultrasonic testing are used to assess the quality of concrete and to identify cracks in large structures, such as bridges and buildings.
Oil and Gas: Inspection of pipes and equipment on oil platforms is essential to prevent failures that could result in leaks or serious accidents.
Automotive: NDT is used to ensure the quality of critical parts, such as axles, engines, and suspension systems, increasing vehicle safety.
These methods not only ensure material quality but also help extend equipment lifespan, minimizing unexpected maintenance costs and preventing catastrophic failures. Click here for NDT Safety Course
Non-destructive testing (NDT) is an essential tool in modern engineering, enabling the safe evaluation of materials and components without compromising them. Since its inception in the early 20th century, these techniques have evolved and become indispensable in various industrial sectors. Professional training is key to ensuring the effectiveness of NDT, making education and ongoing training essential for maintaining high safety and quality standards.
The continuous evolution of NDT technologies offers new possibilities for the future, enabling engineering and related fields to continue achieving higher levels of precision and reliability in the evaluation of materials and structures.